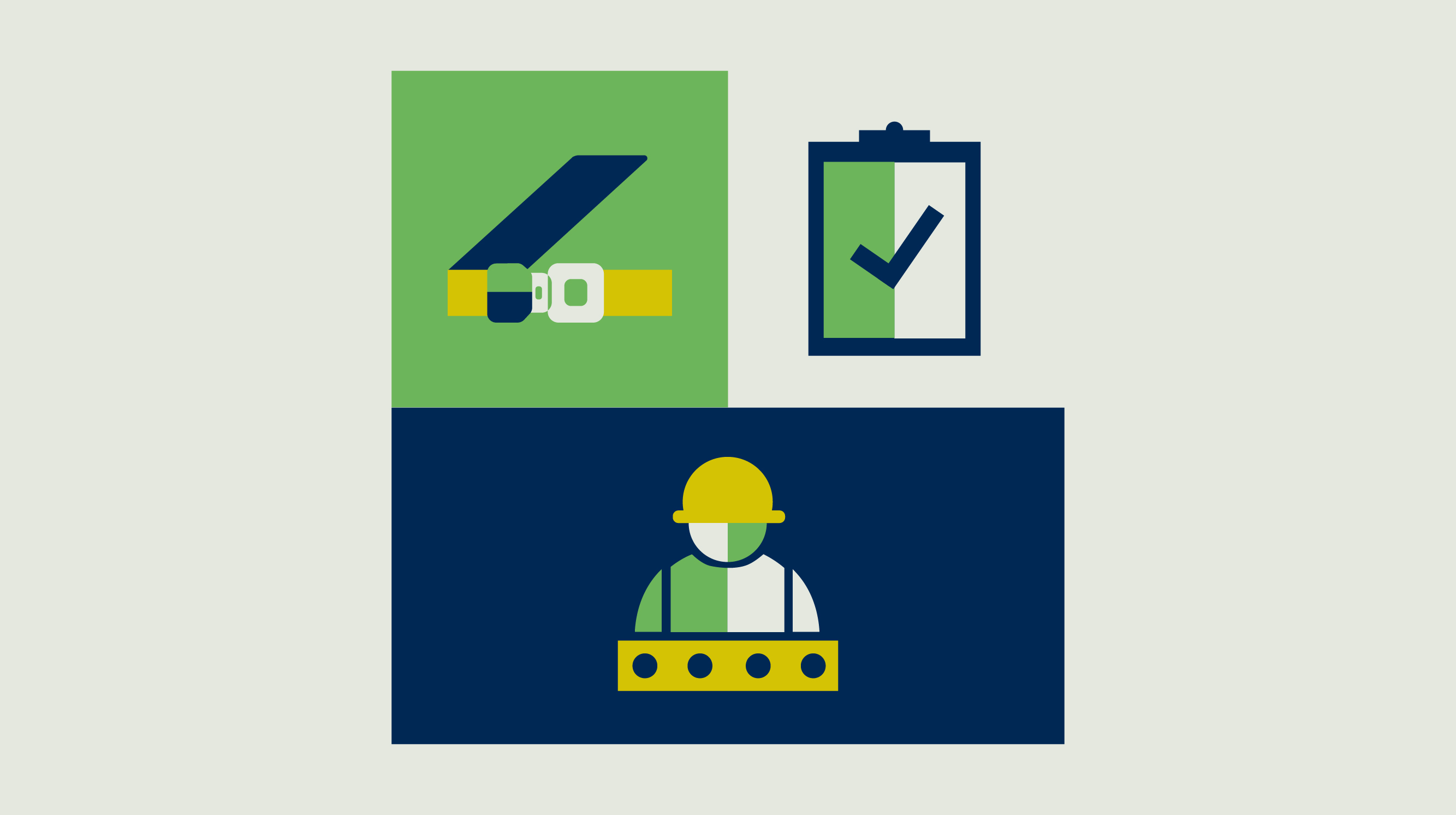
Workplace safety at Teys is about much more than avoiding injuries and ticking a series of check-boxes – “it’s the most important thing we can do”, according to Group Work Health & Safety Manager, Julia Teys.
“When it comes to safety, it’s easy to assume that everything is going well when people aren’t getting injured,” Julia said.
“At Teys, we don’t fall into this trap – we are always looking for areas where we can improve safety, whether that is through engaging and communicating with our workers, or exploring innovation to make manual tasks safer.”
Julia said Teys featured a positive safety culture that empowered everyone across the organisation “to keep our people safe.”
“Our people are our biggest asset – without them we wouldn’t have a business. So it’s our responsibility to do everything possible to keep them safe while at work and send them home to their family at the end of the day,” Julia said.
“Teys is like one big family, so the last thing we want is to see anyone get injured.”
“We promote a reporting culture and learn from our people. Our leaders genuinely care about the wellbeing of our workers and when this is being driven from the top, it then becomes second nature.”
Julia brings 15 years’ experience in workplace health and safety to her role. Previously she worked as the Safety Manager at Teys’ Rockhampton plant, and an inspector and investigator with the Queensland Workplace Health and Safety regulator. She took up her current position in 2017.
“I’m fortunate to work with an awesome safety team who share my same passion for safety, which makes my job not only easier but also enjoyable,” Julia said.
“I love seeing our people achieve their goals and improving safety across their sites. Our team is always striving to improve and identify a different way of doing safety to continue to promote a positive safety culture within our business.”
Key to Teys’ approach to safety is making procedures meaningful and practical, “so they’re easy for everyone to meet”.
“We have worked hard to standardise systems across the business, implementing an electronic reporting/recording system, improving the way we measure safety performance by removing lost time injury frequency rates and associated data as a safety performance indicator, and implementing a safety leadership program for our managers and supervisors,” Julia said.
Julia is particularly proud of Teys’ safety leadership program, which was recognised in 2019 at the NSCA Foundation national awards.
“This was a great achievement to recognise the hard work our team is putting in to improve our safety culture. I’m proud to work in a business that genuinely puts WHS as its top priority.”
Not content to rest on their laurels, Julia and her team continue to monitor and review Teys’ safety systems to ensure industry best practice.
“We focus on developing strategic initiatives to maintain continuous improvement for all WHS systems and programs.”
To find out more about Teys’ safety commitment and initiatives go to https://au.teysgroup.com/our-promise/workplace-health-and-safety/